Solvent welding, socket or butt welding, threading, flanging: consult all the jointing procedures of the different thermoplastic materials
Solvent welding
Solvent welding is the specific longitudinal jointing system for connecting rigid PVC-U or PVC-C pipes and fittings.
Gluing is carried out using special glues/adhesives obtained by dissolving the polymer in a special mixture of solvents, which soften the walls of the pipes and fittings, to then carry out the welding by releasing the material contained therein.
Chemical welding makes it possible to obtain permanent joints with characteristics of chemical and mechanical resistance similar to those of the pipes and fittings used.
The adhesives must be selected according to the type of thermoplastic resin to be welded, since the nature of the solvents and the filler material they contain varies.
Download the pdf for further technical specifications on the insertion length, the beveling of the tube, the characteristics and dimensions of the applicator brushes, the theoretical glue consumption as well as a practical checklist of the most common defects and how to avoid them.
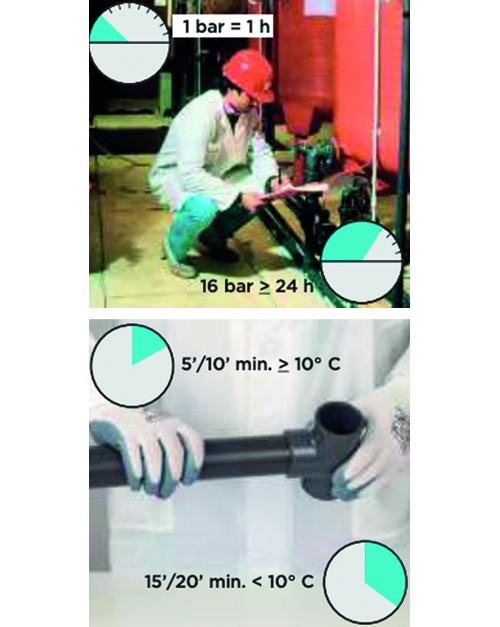
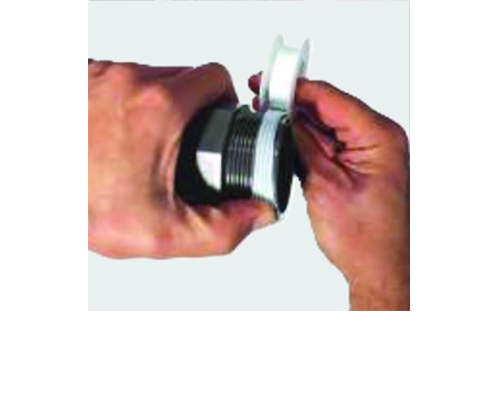
The threaded joints
To guarantee the hydraulic seal of the joint of fittings and valves with threaded ends, it is advisable to carry out a correct sequence of specific operations using only tape
sealant in unsintered PTFE.
It is absolutely to avoid the use of materials such as hemp, fluff or paints normally used to make the hydraulic seal on metal threads.
This type of joint is inadvisable on systems subject to mechanical and/or thermal stresses for which the use of adhesive joints, heat welding or flanged joints is instead recommended.
The flanged joints
To ensure the correct installation of the flanged components, it is recommended to carry out all the necessary operations paying particular attention to checking the tightening torque, the minimum length of the bolts and bolts, both in the case of flanging pipes using free flanges and with fixed flanges to ensure the correct alignment of the drilling with the counterflange.
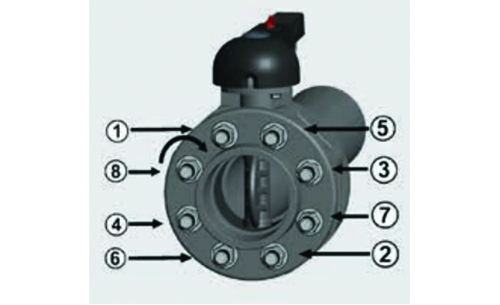
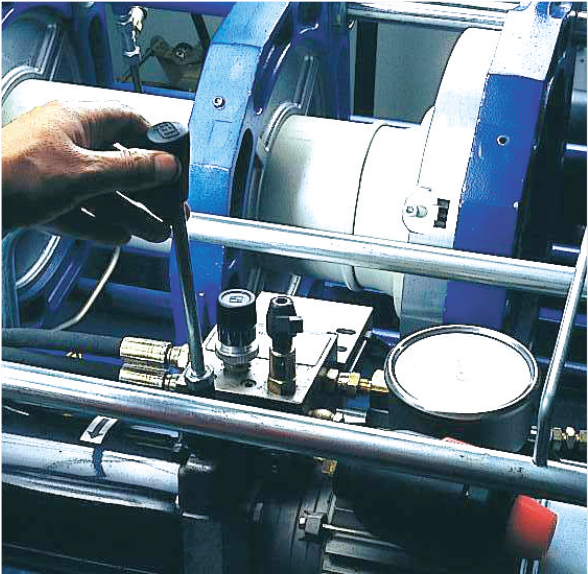
Butt welding
The "butt" welding process, with thermal elements by contact, is the process of joining two elements (pipes and/or fittings) of the same diameter and thickness in which the surfaces to be welded are heated until they melt by contact with a thermal element and subsequently, after its removal , they are joined by pressure to obtain welding.
Installers must be adequately trained and know in depth the correct procedure to follow according to the welding machine being used.
Socket welding
Thermal socket welding involves melting the pipe inside the socket of the fitting.
The joint is obtained by simultaneously melting the male and female surfaces to be welded using special manual or automatic heating equipment.
These machines are, in their simplest form, made up of a thermal plate on which casting sleeves are mounted.
An adequate heating system, equipped with an automatic temperature controller completes the equipment.
No filler material is required to perform the thermal welding. Thermal socket welding does not decrease the degree of chemical resistance of the polypropylene and maintains the internal pressure resistance requirements of the pipes and of the coupled fittings unchanged.
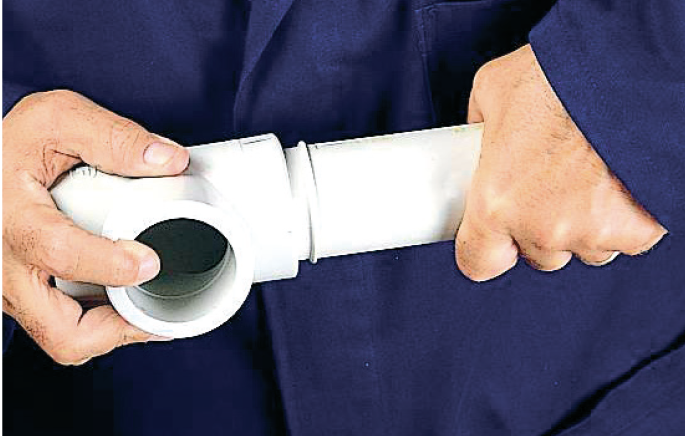